Process Mapping: Your path to process perfection.
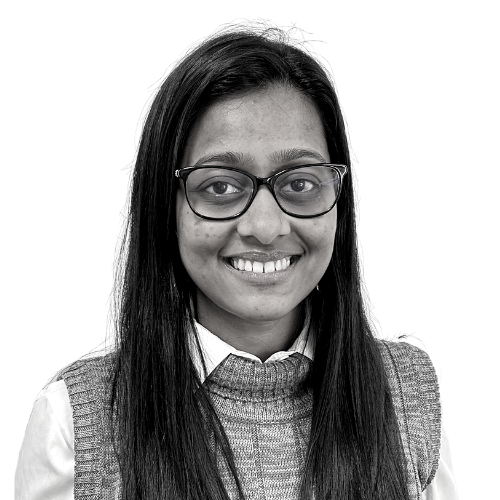
Consultant Keshala Wickrama Gunaratne explores the optimal approach to enhancing your processes.
Process Mapping – the best way to improve your processes.
In today’s business world, we frequently hear terms like ‘Process Improvement’, ‘Continuous Improvement’ and ‘Lean Six Sigma’. But have you ever questioned where you could utilise these in your own business functions?
When you break down your fundamental building blocks, businesses operate as a series of activities or processes. If you can get a clear understanding of these processes and how they interact with one another, you can streamline your business operations, making them more efficient and less prone to error. This is where process mapping comes in.
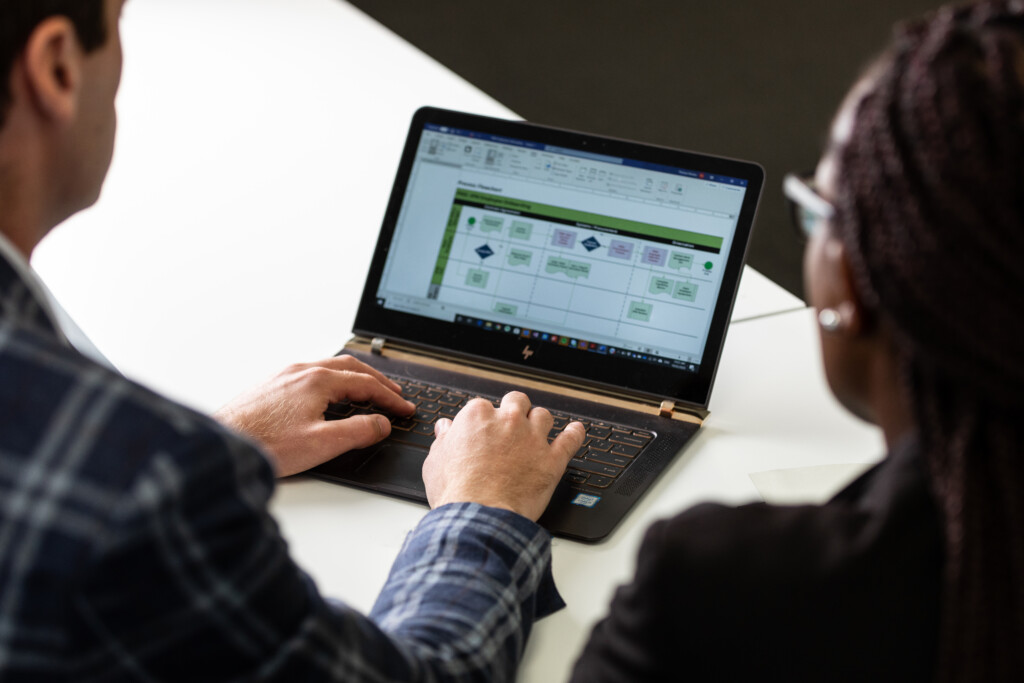
Process mapping is a strategic tool that can help you visualise your business processes and how they interact with one another. By creating a process map, you can identify bottlenecks and areas for improvement and make better informed decisions on how to optimise your operations.
Why use process mapping?
A map is worth a thousand words and when it comes to process maps, they enable us to display workflow steps in a clearer and more concise way.
Highlight areas that need improving.
Process mapping serves as a valuable tool for pinpointing areas of concern. Once these areas are identified, organisations can initiate measures to enhance their operations. This might involve introducing an additional quality control step or implementing new software for task automation. Regardless of the remedy, process mapping aids in the identification of areas requiring improvement.
Boost efficiency and productivity.
By creating a standard map for all employees to follow, you can ensure a level of consistency and efficiency no matter where someone is working. This is where process mapping can be especially helpful for businesses with multiple locations or departments.
Encourage communication and collaboration.
This tool can help all team members to see the big picture. It helps them to understand their role within the business by providing a visual representation of how tasks are interconnected, which makes it easier to communicate with one another and identify potential bottlenecks.
Facilitate change.
Having your processes documented helps you to evolve over time with the introduction of new technologies and methods. By creating a map that can be easily updated, you’ll save time and effort, and not have to start from scratch, every time something changes.
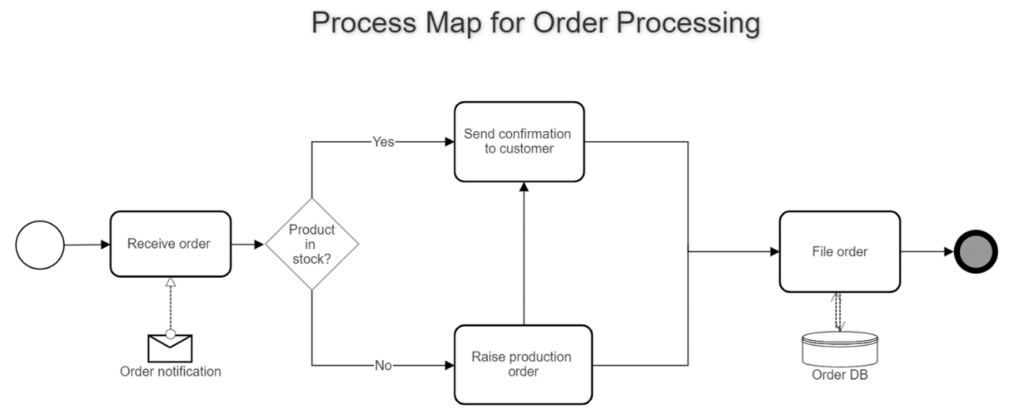
Figure 1: A simple visual illustration of an order processing function
What are the common steps to follow?
Even though there are different ways to improve a process depending on your goals and situation, some common steps are:
- Choose a process to improve, define the scope, and identify stakeholders.
2. Conduct a brainstorming session to gather information.
3. Map out the current state and validate the process.
4. Identify bottlenecks and areas for improvement.
5. Map out the potential new processes and test them.
To sum it up, process mapping is your starting point for breaking down complex workflows, grasping the current situation, and spotting chances for improvement. With visual representations, process maps shed light on where things can be streamlined and where processes might need a little extra attention.
Want to know more? Call us on 03 6105 0546 or email us at [email protected].
Did you enjoy this article? Explore more topics on our Experience page.